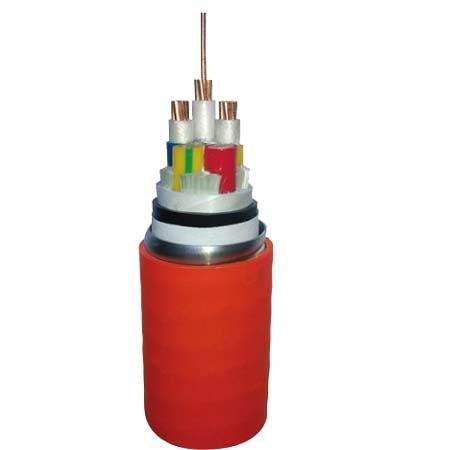
Complete knowledge of cable
External cable route design
Cables are used to transmit electric energy, which is less damaged by external wind, rain, hail and human activities. Both material and installation costs are high, because the efficiency of transmitting electric energy with metal materials of the same cross-section for heat dissipation is not as high as that of overhead lines. It does not occupy land and is conducive to beautiful environment.
Cable construction
Cables can be divided into power cable Control cable, telephone cable, RF coaxial cable, mobile flexible cable, etc.
The basic structure of the cable is mainly composed of three parts: the conductive wire core is used to transmit electric energy; The insulation layer ensures the transmission of electric energy along the core, electrically isolating the core from the outside world; The protective layer plays the role of protection and sealing, so that the insulation layer will not be immersed by moisture, will not be damaged by the outside, and will maintain the insulation performance. The cable structure is shown in Figure 10-10.
1. Cables are classified according to voltage level
Power cables are generally manufactured according to a certain voltage level, and the voltage levels are 0.5kV, 1, 3, 6, 10, 20, 35, 60, 110, 220 and 330kV in turn. Among them, 1kV voltage grade power cables are used most frequently. 3~35kV power cables are often used for main power supply lines in large and medium-sized buildings. 60~330kV power cables are used in power transmission lines that are not suitable for overhead conductors, river crossing, submarine laying, etc. According to the rough classification of voltage, it can be divided into low-voltage cables (less than 1kV) and high-voltage cables (more than 1kV). Considering the construction technical requirements, cable joints, structural characteristics of cable terminals and operation and maintenance, it can also be divided into low-voltage power cables, medium voltage power cables (1-10kV) and high-voltage power cables.
2. Cables are classified according to the sectional area of wire core
The conductive core of power cable is manufactured according to the nominal sectional area of a certain grade, which is convenient for manufacturing, design and construction selection. The nominal sectional area series of power cables in China are 2.5, 4, 6, 10, 16, 25, 35, 50, 70, 95, 120, 150, 185, 240, 300, 400, 500, 600 mm2, a total of 19 types. The nominal sectional area series specifications of high-pressure oil filled cables are 100, 240, 400, 600, 700, 845mm2, totally 6 kinds. Multicore cables are subject to the phase line with the largest section.
3. Classification according to the number of conductor cores
There are five types of conductive core wires of power cable, namely 1-5 cores. Single core cable is used to transmit single-phase AC, DC and special occasions (HV motor outgoing line). Oil filled and gas filled high-voltage cables of 60kV and above voltage levels are mostly single core. Two core cable is usually used to transmit single-phase AC or DC power. Three core cables are used in three-phase AC power networks, and are widely used in cable lines below 35kV. Four core cables are used for low-voltage distribution lines, TT and TN-C power supply systems with neutral grounding. Five core cable is used for TN-S power supply system with low-voltage distribution lines and neutral grounding. Two core and four core cables are low-voltage cables below 1kV.
4. Classification according to insulation materials
Oil impregnated paper insulated power cable: it has the longest history, the most widely used and the most commonly used cable, with low cost, long life, stable heat resistance and electricity resistance. It is widely used in various low-voltage power cables. It is usually made of paper as the main insulation and fully impregnated with insulation impregnant. According to different impregnant conditions and insulation structures, it can be divided into the following categories. For ordinary adhesive impregnated paper insulated cables, the impregnant is a viscous impregnant mixed with low-voltage cable oil and rosin. According to different structures, it can be divided into turnkey type, split phase lead (aluminum) wrapped type and split phase shielded type. Plastic insulated cable: plastic insulated cable is simple to manufacture, light in weight, easy to manufacture terminal head and intermediate head, small in bending radius, easy to lay, easy to maintain, has certain chemical corrosion resistance and water resistance, and is used in high drop and vertical laying occasions. Plastic insulated cable PVC insulated cable And XLPE insulated cables. The former is used in cable lines below 1kV, and the latter is used in cable lines from 10kV to high voltage. Rubber insulated cable: because rubber is elastic, stable and has good electrical, mechanical and chemical properties, it is widely used in cables below 1kV. Flame retardant PVC insulated cable: the common disadvantage of the first three types of cables is that the materials are combustible. When an accident occurs in the line or at the joint, the cable may burn due to local overheating, expanding the scope of the accident. Flame retardant cable is added with flame retardant in PVC, so it will not burn even if it is barbecued with open fire. It is a kind of plastic cable, which is used in cable lines below 10kV.
The design safety factor of insulated conductor and steel strand hanging insulated conductor shall not be less than 3. The dead weight load of the steel strand hanging insulated wire shall include the mass of insulated wire, steel strand, insulated support and 200kg construction load. The minimum section of steel strand shall not be less than 50mm2. Wires of different metals, different specifications, and different twisted directions, as well as bundled wires without load-bearing wires, are strictly prohibited from being connected within the span. Within a span, each conductor shall not exceed one load-bearing joint. The distance between the connector and the fixed point of the conductor shall not be less than 500mm. The safety factor of the insulation support shall not be less than 5, and the breaking force of the insulation rod shall not be less than 90% of the calculated breaking force of the conductor. And the damage stress of insulation support and insulation pull rod shall meet the requirements of maximum short-circuit electrodynamic force.
10.2.2 Cable specifications
1. Rated voltage
The rated voltage depends on the phase to phase voltage of the cable system, the type of the system, the troubleshooting time of the protective equipment, etc. In the ungrounded system, the cable will run for a long time in case of single-phase grounding fault. However, the voltage gradient between two lines will be generated between the insulation of the other two ungrounded conductors, and the insulation layer is required to be thicker. It is impossible to apply all line to line voltages for a long time between fault free two phases. If the protection equipment can remove the fault within 1min, then cables with 100% rated voltage can be selected in this grounding system. For ungrounded system, when the 1min clearing time specified for 100% rated voltage level cannot be met, but the fault section can be cleared within 1h, 133% rated voltage cable shall be selected. When the time for clearing the grounding fault section is quite long, 173% rated voltage level insulation shall be selected.
2. Selection of wires
When selecting conductor specifications, the following shall be considered: requirements of the national electrical code, thermal effect of load current, mutual heating effect, loss caused by electromagnetic induction, dielectric loss, load current related indicators, emergency overload indicators, voltage drop limit and fault current indicators.
3. Load current index
The ampacity table lists the minimum size of the wires required. However, the cable selection in the project is often conservative, which takes into account the load growth, voltage drop, short circuit current heating and other factors.
4. Emergency overload index
The normal load limits of insulated wires and cables are based on practical experience and represent the aging speed of cables. This aging rate is expected to make the effective life of the cable last 20-30 years. When the normal daily load temperature increases by 8 ℃, the average failure rate will be doubled, and the insulation life of the cable will be shortened by half. It is an extraordinary measure for cables to operate continuously when the maximum rated temperature or rated current carrying capacity is exceeded. The temperature rise is proportional to the wire loss, and the loss increases with the square of the current. A large voltage drop may cause unexpected danger to the continuity of equipment and power supply. The cable shall operate under the maximum emergency overload temperature, and the overload period of 100h shall not exceed five times within the service life of the cable. Overload coefficient of various insulated cables with short-term overload. The emergency or overload current value of this insulated cable can be obtained by multiplying the overload coefficient by the nominal rated current value of the cable.
5. Voltage drop index
If the section of the power supply line is not large enough, excessive voltage drop will occur in the circuit. The voltage drop is proportional to the line length. Considering the normal starting and operation of motor, lighting equipment and other loads with large impact current, the specification stipulates that the steady-state voltage drop of power, heating or lighting feeders shall not exceed 3%, and the total voltage drop, including feeders and branch lines, shall not exceed 5%. In the case of a short circuit, the temperature of the conductor rises rapidly. However, due to the thermal characteristics of cable insulation, sheath, coating materials, etc., the cooling process of the conductor is slow after the short circuit is eliminated. Failure to pay attention to the thermal stability of the cable will cause permanent damage to the cable insulation due to the deterioration of the insulation material, which may be accompanied by smoke and combustible gas. If there is enough heat, these gases will ignite and cause a serious fire. Even if the degree is not so serious, it may cause the insulation or sheath of the cable to expand, resulting in gaps, which may lead to failure. This is particularly serious for high-voltage cables. In addition to thermal stress, thermal expansion also generates mechanical stress in the cable. These stresses may cause undesired cable movement due to sharp heating. However, the new cable strengthens the binding and sheath, significantly reducing the impact of this stress. When selecting and using cables within the predetermined temperature range, it is generally unnecessary to pay attention to their mechanical characteristics, unless the cables are very old or lead coated. In case of short circuit or large impulse current, single core cable will bear mutual repulsion or attraction between cables. In order to prevent cable damage caused by such movement, the cable laid on the cable support or cable tray shall be fixed.
10.2.3 Service conditions of cables
When a large number of cables are laid in groups, the current carrying capacity of the cables is reduced due to the mutual heating effect. Sometimes, two or more parallel cables with smaller specifications need to be considered to replace cables with larger specifications, because large cross-section cables will reduce the current carrying capacity of unit cross-section due to skin effect and proximity effect. On the other hand, the reduction of the ratio of the surface area to the cross-sectional area of the large cross-section cable makes the heat dissipation capacity of the large cable poor. If multiple cables are used in parallel, the relative position of each cable shall be considered to reduce the uneven distribution effect of cable current carrying capacity.
For cables laid in underground pipelines, when using the load factor, the heat capacity of the average heat loss of the pipe group and the surrounding soil should be considered. The temperature of the underground part changes with the change of the average heat loss, so it is allowed that the higher short-term load coefficient is the ratio of the average load to the peak load, which is usually measured based on the day and night average load. The peak load generally refers to the average value of the maximum load occurring within 24h and 0.5~1h. For directly buried cables, the average surface temperature can be limited to 0~60 ℃ according to the soil conditions to prevent the loss of soil moisture and thermal breakdown of cables. When the cable is close to other loaded cables or heat sources, or when the ambient temperature exceeds the ambient temperature of the specified cable ampacity, the rated ampacity of the cable must be reduced. The normal ambient temperature of the cable device refers to the temperature where the cable is installed when the cable is not loaded. In order to properly determine the cable specification required for a given load, this temperature should be thoroughly understood. For example, the ambient temperature of a cable laid separately from other cables in the air refers to the temperature before the cable is loaded. For cables in the air, it is also assumed that there is enough space around the cable to distribute the heat generated by the cable, and the temperature of the whole room will not be increased. If the above correct conditions are specified, the following environmental conditions can be used to calculate the current carrying capacity of the cable.
Cable lines shall be used for urban high and medium voltage distribution lines in the following cases. Prosperous urban areas, important sections, main roads, and areas with special requirements for urban planning and city appearance and environment; Severe corrosion sections that are difficult to solve technically; Sections of key scenic spots; Important power supply sections of major coastal cities vulnerable to salt pollution or tropical storms; Other sections required for grid structure and operation safety. The urban central area with high cable line load density shall be used for urban low-voltage distribution lines in the following cases:; New residential quarters and high-rise building quarters with large construction area; According to the planning, the streets or areas where overhead lines are not suitable and the areas where incoming and outgoing lines are crowded; After technical and economic comparison, other conditions that are more suitable for the use of electric county regiment level lines are adopted. If the cable line should be used and the underground conditions are not available, the insulated cable can be laid overhead.
Indoor For low-voltage cables, the ampacity meter in the national electrical regulations is based on the ambient temperature of 30 ℃. However, in summer months in most areas, 40 ℃ is appropriate for at least some parts of buildings. When determining the current carrying capacity of the cable, the heat source that is most unfavorable to the cable nearby must be considered. The local overheating of the cable may be caused by the steam pipe or the heat source near the cable, or it may be caused by the cable passing through the boiler room or other high temperature places. To avoid such problems, it may be necessary to reroute.
For outdoor cables installed in shade, the maximum ambient temperature is generally 40 ℃, while for cables installed in sunlight, the maximum ambient temperature is generally 50 ℃. When using these ambient temperatures, it is assumed that the maximum load occurs exactly at the specified ambient temperature. During the hottest time of the day, or when the sun shines hardest, some circuits are not running at full load. Under such conditions, it is reasonable for outdoor cables to adopt an ambient temperature of 40 ℃ in terms of safety.
Underground In different areas of a country, the ambient temperature for underground cables varies. In northern China, the ambient temperature is usually 20 ℃, and in central China, it is 25 ℃; For the southernmost and southwest ends, the ambient temperature may be 30 ℃. It is impossible to precisely delineate the geographical boundaries of these ambient temperatures. The maximum ambient temperature can be measured at a point away from the heat source and at the depth of the buried cable. The change of soil ambient temperature will lag behind the change of air temperature for several weeks.
When determining the current carrying capacity of the cable, the thermal performance of the medium around the cable is an important parameter. The type of soil in which cables or cable pipe blocks are buried has a significant impact on the current carrying capacity of cables. Porous loose soil, such as gravel and ash backfill, usually has higher temperature and lower carrying capacity than sand or clay. Therefore, before calculating cable specifications, it is necessary to know the type of soil and its thermal resistivity. The water content of the soil also has an important impact on the current carrying capacity of the cable. In dry areas, in order to compensate for the increase of thermal resistance due to lack of moisture, the rated current carrying capacity of the cable must be reduced or other preventive measures must be taken. On the other hand, in the often humid underground or tidal affected areas, the cable can pass a current larger than the normal current. For places that are often wet or alternate between wet and dry, and where there is a transition from dry cables to "naturally shielded" wet cables, even high-voltage lines need shielding. Because there will be sudden change of voltage gradient stress in these places, unless it is an unshielded cable specially designed for this purpose.
When directly buried in the frozen soil area, it should be buried below the frozen soil layer. When it is impossible to bury deeply, it can be buried in the dry frozen soil layer or backfill with good soil drainage, or other measures can be taken. Cables directly buried shall not be located directly above or below underground pipelines. 0.25m separated by partition; 0.1m for cable threading; It can be reduced in special circumstances. When directly buried in non frozen soil areas, the burial depth of cables shall not be less than 0.3m from the cable sheath to the foundation of underground structures. When the directly buried cable crosses the railway, highway or street, it shall pass through the protective pipe, and the protection scope shall exceed the subgrade, both sides of the street pavement and the drainage ditch for more than 0.5m. For directly buried cable entry structures, protective pipes shall be set at the wall holes, and the pipe orifices shall be blocked. For the joint configuration of directly buried cables, the clear distance between the joint and adjacent cables shall not be less than 0.25m. The joint positions of parallel cables should be staggered with a clear distance of not less than 0.5m. The joints at the slope terrain shall be placed horizontally. For the cable joints of important circuits, it is advisable to lay cables in the local section starting from about 100mm on both sides in the way of reserving reserve. When special soil replacement and backfilling are adopted for directly buried cables, the soil quality of the backfill shall be non corrosive to the cable outer sheath.
10.2.4 Type of cable sheath
Although the manufacturing should follow the national standards, there were three core cables used for AC single-phase situations in the project, and the case of excessive temperature rise of cables due to eddy current loss heating occurred. The bare lead wrapped cable is directly buried in wet soil and has corrosion perforation; Although the coat armor has a certain anti-corrosion effect, it will rust after a long time in the chemical corrosion environment.
Polyethylene PE or polyvinyl chloride PVC are commonly used for cable extrusion jacket. Polyethylene PE is not as good as polyvinyl chloride (PVC) in resistance to environmental stress cracking. The chlorine decomposed by PVC during combustion is helpful for flame retardancy, and PVC is mostly used. However, ordinary PVC is prone to embrittlement and cracking at low temperatures below - 20 ℃, while polyethylene can withstand - 50~- 60 ℃; Polyethylene is superior to PVC in resistance to acetone, xylene, chloroform, petroleum ether, creosote oil, sodium hydroxide and other chemicals; When burning, polyethylene does not release toxic gases such as hydrogen chloride like PVC. In these cases, polyethylene should be used as extrusion sheath. One of the conditions for directly buried laying, such as steel strip armouring. Due to the high pressure transmitted to the cable when heavy vehicles pass through. Referring to the technical standards of Japanese electrical equipment, the burial depth of direct burial laying is required to be more than - 1.2m for the section where the truck passes, except that the burial depth can be - 0.6m without heavy pressure, and it is allowed to use the cable without steel tape armouring, while the general burial depth of cables of 35kV and below is required to be not less than - 0.7m. The use of steel armoring for direct buried laying is also considered to prevent external force damage.
Statistics show that there are many accidents of directly buried cables, and the proportion of mechanical damage is quite high. It is not uncommon for all plastic cables to be damaged by rats and lead to failures. Statistics show that cables with an outer diameter of 10~15mm suffer the most damage. Electric signal accidents caused by rats in Japanese railways occurred 335 times from 1969 to 1984, up to 48 to 62 times a year. The underwater cable is mainly under the stress conditions of water depth, long underwater, high water flow speed, wave, tide and other combined effects. The tension resistance of cable core alone is often not enough to meet the requirements. It needs steel wire armoring and should be pre twisted or twisted in the opposite direction. In addition, the anchoring of river and sea vessels and fishing gear of sea trawlers may be in danger of mechanical damage, and sometimes cables need to have appropriate protective characteristics. There may also be double-layer steel wire armouring, steel tape plus double-layer steel wire armouring, or reverse wound double-layer steel wire, short pitch wound double-layer steel wire, and load bearing wire made of polyamide fiber in the armouring SiC PVC sheath and other structural types can be selected according to local conditions.
10.2.5 Cable shielding
1. Shielding definition of power cable
Enclose the electric field of the cable in the insulating layer surrounding the conductor with a conductive or semi conductive layer. The conductive or semiconducting layer is closely attached to the inner and outer surfaces of the insulation. In other words, the external shield encloses the electric field between the conductor and the shielding layer. The internal shield or stranded stress relief layer is at or near the potential of the conductor, and the external shield or insulation shield is designed to transmit capacitive current, and in many cases is also used to transmit fault current. The conductivity of the shielding layer is determined by the cross-sectional area and resistivity of the metal belt or wire used together with the semiconducting layer. The stress control layer on the inner and outer surfaces of the insulation is a smooth surface close to the insulation surface, thus reducing the stress concentration and minimizing the gap. In this gap, the ionization of air may gradually damage some insulating materials until they are completely damaged.
2. The insulation shield has various uses
Enclose the electric field inside the cable; Balance the voltage gradient inside the insulation to minimize the surface discharge; Avoid induced potential to better reduce the risk of electric shock. The voltage distribution between the unshielded cable and the grounding plane, assuming that the air and insulation are the same in terms of electrical performance, the cable above the grounding plane is in uniform dielectric, so it is allowed to use simple diagrams to illustrate the voltage distribution and electric field related to the cable. In the shielded cable, the equipotential surface between the conductor and the shielding layer is a concentric cylindrical surface, the voltage distribution changes according to a simple logarithmic law, and the electrostatic field is all enclosed in the insulation layer. The power line and stress are uniform, radiating, intersecting at right angles to the equipotential surface, which eliminates the tangent stress or longitudinal stress in the insulation or on the insulation surface. The equipotential surface of the unshielded system is cylindrical, but not concentric with the conductor. It intersects the cable surface with many different potentials. For unshielded cables running high systems, the tangential leakage stress to the ground at each point of the cable may be several times the normal recommended leakage distance of the cable terminal in a dry place. In this case, surface leakage traces, combustion and destructive discharge to the ground may occur. However, the properly designed unshielded cable described in the national electrical regulations limits the available surface energy, which comes from these effects and may affect the normal use of the cable.
For cables with operating voltage below 1kV, the unshielded structure is generally used. For cables with operating voltage above 10kV, it is necessary to shield them to comply with the national electrical regulations. Shielded and unshielded cables are allowed to be used within the range of 1~10kV, as long as their structures can meet the requirements of national standards. Because the price of shielded cable is generally higher than that of unshielded cable, and because the production of shielded cable terminal requires more care and more space, unshielded cable has been widely used in the range of 1~10kV, and unshielded cable is also widely used in 10kV voltage level. However, shielded cables can be designated to be used in places directly buried underground or where a large amount of conductive materials (salt, soot, conductive grease for pipe threading) may accumulate on the cable surface.
3. Control cable and its metal shield
The control cable shall not be affected by insulation damage, mechanical damage, fire or electrical interference. The current, voltage, DC power supply, tripping control circuit and other systems requiring enhanced reliability of dual protection shall use their own independent control cables. The following circuits should not share the same control cable: weak current signal, control circuit and strong current signal, control circuit; Low level signal and high level signal circuit; The weak current control circuit of each phase of the AC circuit breaker is operated separately. The distance between the cores of the same cable is small, the coupling and electromagnetic induction are strong, and the interference between cables is greater than that between cables. The analog low level signal line of the computer monitoring system in a power plant shares a four core cable with the transmitter power line, which causes the signal line to generate about 70V common mode interference voltage, obviously affecting the normal operation of the low-level signal circuit in millivolts.
Each pair of round trip conductors of weak current circuit should belong to the same control cable. The strong current circuit control cable can be free of metal shielding, except when it is located in the ultra-high voltage power distribution device or adjacent to the high voltage cable and needs to suppress interference. When the control cable of weak current signal and control circuit is located in an environment with interference and without effective anti-interference measures, it should be shielded with metal. The selection of metal shielding type of control cable shall include comprehensive interference suppression measures according to the possible electrical interference effects to meet the requirements of reducing interference or overvoltage. The weak current control cable located in the power distribution device above 110kV should have a general shield and a double-layer general shield. For the shielding selection of control cable of signal circuit of computer monitoring system, the total shielding can be used for switching value signal. For high-level analog signals, it is better to use twisted pair cores for overall shielding, or use twisted pair cores for sub shielding if necessary, while for low-level analog signals or impulse signals, it is better to use twisted pair cores for sub shielding, or use twisted pair cores for sub shielding and composite overall shielding if necessary. In other cases, appropriate shielding type shall be adopted according to the influence factors of electromagnetic induction, electrostatic induction and ground potential rise.
For control cables that need to reduce electrical interference, a grounded spare core can be added to the number of working cores. When one core of control cable is grounded, the amplitude of interference voltage can be reduced to 50%~25% or more, and the implementation is simple, with little increase in cable cost. For the grounding mode of the control cable metal shield, the control cable shield layer of the analog signal circuit of the computer monitoring system shall not form two-point or multi-point grounding, and the centralized one point grounding is preferred. In addition, the shielding layer of control cable other than one point grounding is required. When the interference of electromagnetic induction is large, two point grounding should be adopted; The interference of electrostatic induction is large, so it can be grounded at one point. For double shielding or composite general shielding, it is better to use one point for internal and external shielding respectively, and two points are grounded. The selection of two-point grounding should also consider that the shielding layer will not be fused under the action of transient current.
If the same round-trip conductor belongs to two cables, it is difficult to avoid the possibility of forming a ring when laying it. Potential will be induced under the cross chain of electromagnetic wires of similar power sources, and its order of magnitude often has a greater impact on the interference of low-level parameters of weak current circuit. If the weak current circuit control cable and power cable can be pulled apart sufficiently, or laid in steel pipes, steel enclosed trays, etc., the external interference may be reduced to the allowable limit. Otherwise, it is generally laid in parallel adjacent to the power cable, or it is located in the high-voltage power distribution device and there is a grounding main line nearby. The interference amplitude will often affect the low-level signal circuit connected to the unshielded control cable, such as maloperation or insulation breakdown. The effect of reducing interference when the control cable contains metal shielding is related to the shielding structure. At the same time, it should be noted that the higher the requirements for shielding structure, the greater the corresponding investment. The cost of control cables with and without metal shielding will increase by 10%~20% (steel tape armouring, steel wire braiding total shielding) or more.
The control cable shield of the digital signal circuit of the electronic device shall be grounded so that the interference effect of the voltage drop on the ground wire shall be as small as possible. Based on the interference voltage of only about 1V such as the computer, it may cause logic errors. Therefore, the requirements for the control cable of the analog signal circuit of the calculation monitoring system to suppress interference shall be emphasized, and one point grounding shall be implemented, One point grounding can be implemented in many ways. The computer monitoring system indicates that the centralized one point grounding can meet the conditions of avoiding grounding circulation. The current distribution of the grounding grid in the power distribution device has measured 13% of the grounding current, and the 110~500kV voltage level short circuit current has reached 35~18kA.
4. Method of shielded cable
Cut off a section of cable shielding layer at the end of the cable, and leave necessary leakage distance between the conductor and the shielding layer, which will form longitudinal stress on the exposed cable insulation surface. The combined effect of radial and longitudinal electrical stresses on the cable end termination device will result in the maximum stress at this point. However, these stresses can be controlled and reduced to the safe working range of the materials used to make the terminal device. The most common way to reduce these stresses is to gradually increase the total insulation thickness of the cable terminal device with insulating tape to form a cone, that is, a stress cone. In China, three types of distribution network cables are mainly used: adhesive impregnated oil paper insulated cable, PVC cable, cross-linked polyethylene cable and cross-linked polyethylene cable. Viscous impregnated oil paper insulated cables have the advantages of high allowable operating temperature, low dielectric loss, high voltage withstand strength, and long service life. Their disadvantages are poor bending performance of insulating materials, which cannot be laid at low temperatures. According to the impregnation method, there are three types of ordinary oil paper insulation, drip type oil paper insulation, and non drip type oil paper insulation, It can be used according to the horizontal height difference of cable laying. The horizontal elevation difference of ordinary oil immersed paper insulated cable laying is only allowed to be 5~20m, the horizontal elevation difference of drip dried oil immersed paper insulated cable laying is allowed to be 100~300m, and there is no height difference limit for non drip dried oil immersed insulated cable laying. The main advantages of PVC cable are simple manufacturing process, no height difference limit for laying, good bending performance, oil resistance, acid and alkali resistance, no flame retardance, and low price. The disadvantage is that the insulation resistance is lower than that of oil impregnated paper insulated cable, and the dielectric loss is high, so it is not suitable for use on important 6kV lines. XLPE cable is widely used in distribution network due to its excellent performance, simple structure, light weight, large current carrying capacity, convenient laying and no height difference limitation.
(1) The concept of wires and cables and the distinction between wires and cables:
Wires and cables refer to materials used for power, communication and related transmission purposes. There is no strict boundary between "wire" and "cable". Generally, products with few cores, small diameter and simple structure are called wires, those without insulation are called bare wires, and others are called cables; The conductor with large cross-sectional area (more than 6 mm2) is called large wire, the smaller one (less than or equal to 6 mm2) is called small wire, and the insulated wire is also called Wiring 。
Wires and cables mainly include bare wires, electromagnetic wires, insulated wires for motors and electrical appliances, power cables, communication cables and optical cables.
Wire and cable naming:
The complete naming of wires and cables is usually complicated, so people sometimes use a simple name (usually a category name) in combination with the model and specification to replace the complete name. For example, "low-voltage cable" represents all plastic insulated power cables of 0.6/1kV class. The type spectrum of wires and cables is relatively complete. It can be said that as long as the standard models and specifications of wires and cables are written, the specific products can be identified, but what is the complete name of them.
The naming of wire and cable products has the following principles:
1. Contents included in the product name
(1) Name of product application or size category
(2) Product structural material or type;
(3) Important or additional features of the product
The names are basically in the above order. Sometimes, in order to emphasize important or additional features, the features are written before or before the corresponding structure description.
2. Sequence of structure description
The product structure is described from inside to outside: conductor -->insulation -->inner sheath -->outer sheath -->armored type.
3. Simplification
In case of no confusion, some structural descriptions are omitted or abbreviated, for example, aluminum conductors are not allowed in automobile wires and flexible wires, so conductor materials are not described.
example:
Rated voltage 8.7/15kV flame-retardant copper core XLPE insulated steel tape armored PVC sheathed power cable
"Rated voltage 8.7/15kV" - application occasion/voltage level
"Flame Retardant" - Highlighted Features
"Copper core" - conductor material
"Cross linked polyethylene insulation" - insulation material
"Steel strip armouring" - armor layer material and type (double steel strip gap wrapping)
"PVC sheath" - inner and outer sheath materials (inner and outer sheath materials are the same, omitting inner sheath materials)
"Power cable" - name of product category
The corresponding model is written as ZR-YJV22-8.7/15, and the model is described below.
model:
The model composition and sequence of wires and cables are as follows:
[1: category, use] [2: conductor] [3: insulation] [4: inner sheath] [5: structural features] [6: outer sheath or derivative] - [7: use features]
Items 1-5 and 7 are represented by pinyin letters, and polymer materials are represented by the first letter of the English name. Each item can be 1-2 letters; Item 6 is 1-3 numbers.
Omission principle in the model: copper is the main conductor material used in wire and cable products, so the code T of copper core is omitted, except for bare wires and bare conductor products. Bare wires and bare conductor products, power cables, and electromagnetic wire products do not indicate the category code, nor do wires and cables for electrical equipment and communication cables, but list the category code or series code.
Item 7 is the mark for various special use occasions or additional special use requirements, which is marked with pinyin letters after "-". Sometimes, in order to highlight this item, write it first. Such as ZR - (flame retardant), NH - (fire-resistant), WDZ - (low smoke and zero halogen, enterprise standard), - TH (used in hot and humid areas), FY - (termite prevention, enterprise standard), etc.
Digital marker
Armor layer
Outer coating or sheath
zero
nothing
---
one
Interlocking armor
Fibrous integument
two
Double layer steel strip
PVC jacket
three
Fine round steel wire
Polyethylene jacket
four
Thick round steel wire
five
Wrinkled (corrugated) steel strip
six
Double aluminum (or aluminum alloy) strip
eight
Copper wire braiding
nine
Steel wire braiding
(2) Common sense of wires and cables 80 Q&A:
1. What kinds of wires and cables are commonly used according to their uses?
Answer: It can be divided into bare wire, insulated wire, heat-resistant wire, shielded wire, power cable, control cable, communication cable, RF cable, etc.
2. What kinds of insulated wires are there?
Answer: There are often several kinds of insulated wires as follows: PVC insulated wires, PVC insulated cords, nitrile PVC mixture insulated cords, rubber insulated wires, agricultural underground directly buried aluminum core plastic insulated wires, rubber insulated cotton yarn textile cords, PVC insulated nylon sheathed wires, PVC insulated cords for power and lighting, etc.
3. Where is the cable tray suitable for?
Answer: The cable bridge is applicable to the indoor and outdoor overhead laying of power cables and control cables in general industrial and mining enterprises, as well as the indoor and outdoor erection of telecommunications, radio and television departments.
4. What are the cable accessories?
Answer: Common electrical accessories include cable terminal junction box, cable intermediate junction box, connecting pipe and terminal, steel plate junction slot, cable bridge, etc.
5. What is a cable intermediate joint?
Answer: The device that connects the cable with the conductor, insulation shield and protective layer of the cable to connect the cable line is called the cable intermediate joint.
6. What is the main electrical wiring?
Answer: The main electrical connection is the connection mode of main electrical equipment and bus in power plants and substations, including the connection mode of main bus and auxiliary power system according to certain functional requirements.
7. What regulations should be followed when selecting the section of power cable?
Answer: The selection of power cables should follow the following principles:
(1) The rated voltage of the cable shall be greater than or equal to the rated voltage of the power supply system at the installation point;
(2) The continuous allowable current of the cable shall be equal to or greater than the maximum continuous current of the power supply load;
(3) Core section shall meet the stability requirements of power supply system in case of short circuit;
(4) Check whether the voltage drop meets the requirements according to the cable length;
(5) The minimum short-circuit current at the end of the line shall enable the protection device to operate reliably.
8. What are the advantages of XLPE cable and oil paper cable?
Answer: (1) It is easy to install because it allows small minimum bending radius and light weight;
(2) Not limited by line drop;
(3) Good thermal performance, high allowable working temperature and large transmission capacity;
(4) Simple cable accessories, all of which are of dry structure;
(5) Simple operation and maintenance without oil leakage;
(6) Low price;
(7) High reliability and low failure rate;
(8) There are few manufacturing processes, simple process, and significant economic benefits.
9. What are the requirements for fixing clamps for AC single core cables? Why?
Answer: The clamp should have no iron parts to form a closed magnetic circuit. This is because when the cable core passes through the current, a magnetic line of force is generated around it. The magnetic line of force is proportional to the current passing through the core. If magnetic conductive materials such as iron parts are used, according to the electromagnetic induction, eddy current will be generated in the iron parts to heat the cable, or even burn the cable. Therefore, iron parts cannot be used as the fixing fixture of single core AC cables.
10. What are the biggest features and advantages of the following accessories of heat shrinkable cable head?
Answer: The biggest feature of heat shrinkable accessories is that the stress tube replaces the traditional stress cone. It not only simplifies the construction process, but also reduces the size of the terminal of the joint. It is easy to install, time-saving, labor saving, superior performance, and metal saving. The heat shrinkable cable accessory integrates the pouring type and the dry wrapping type, which combines the advantages of these two accessories.
11. What inspection work should be carried out before cable laying?
Answer: (1) The support shall be complete and the paint shall be complete.
(2) The cable model, voltage and specification meet the design.
(3) The cable insulation is good. If there is doubt about the sealing of the oil paper cable, it should be judged that the cable is damp; The direct buried cable and small bottom cable shall pass the DC withstand voltage test; The oil sample of oil filled cable shall pass the test.
(4) The oil pressure of oil filled cable should not be lower than 1.47MPa.
21. What are the advantages of cross-linked heat shrinkable cable accessories?
A: This is a new type of material. Compared with other types of accessories, it has the advantages of superior electrical performance, small size, small mass, simple installation, and matching materials. In addition, it also has the ability of weather resistance, pollution resistance, flame retardant and self extinguishing.
12. If there is doubt about the sealing of oil paper insulated power cable, how to check whether the cable insulation paper is damp with a simpler method?
Answer: Ignite the cable insulating paper or put it into the cable oil at about 150 ℃ for inspection. There is no "hissing" sound or white foam, indicating that it is not affected with moisture.
13. What should be indicated on the cable signboard? What are the requirements for writing?
Answer: The signboard should indicate the cable route design number, cable model, specification and starting point, and the cables used in parallel should have a sequence number. The writing shall be clear and not easy to fall off.
14. Where should the direction signs of directly buried cables be set?
Answer: At both ends of the cable, the cable joints at 50~100m of the straight section of the cable and the corners where the cable changes direction.
15. How to remove moisture from yellow wax silk tape, black glass paint tape, alkali free glass ribbon, etc. used for making cable joints before construction?
Answer: (1) Constant temperature drying method: roll the insulating tape into small coils with a diameter of 25~30mm, dry it in a constant temperature drying oven at 110~120 ℃ for 4~5h, cool it dry, take it out, and put it into a dry sealed cylinder.
(2) Oil immersed moisture removal method: put a small roll of insulating tape into the cable oil with a constant temperature of 120~130 ℃, keep a distance of 30mm from the bottom of the pot, take it out after a certain period of time when the oil surface no longer produces foam, and put it into the barrel where the cable oil is stored. The oil level should exceed all the loaded objects and seal them.
16. What is the function of cable sheath?
Answer: Protect the inner protective layer from mechanical damage and chemical corrosion, and enhance the mechanical strength.
17. What requirements should outdoor cable trench meet?
Answer: The upper part of the cable trench should be slightly higher than the ground, covered with a cover plate made of concrete, and the cable should be laid flat on the support with good drainage pipes.
18. What is the function of cable inner sheath?
Answer:; The insulation layer will not contact with water, air or other objects, so as to prevent the insulation from moisture and mechanical damage.
19. What should be paid attention to when using wire cutters?
Answer: Before use, be sure to check whether the insulation of the insulating handle is intact. When using, do not use wire cutters to cut the metal wire beyond the specification. Do not use wire cutters instead of hammers to hit tools to avoid damage.
20. What is insulation strength?
Answer: When an insulating material is in an electric field, it will be broken down when the electric field strength increases to a certain limit. The electric field strength that causes insulation breakdown is called insulation strength.
22. What are the requirements for the mechanical strength of the cable conductor connection points?
Answer: The mechanical strength of the connection point is generally lower than the tensile strength of the cable conductor itself. For fixed power cables, the tensile strength of the connection point is required to be no less than 60% of the tensile strength of the conductor itself.
23. What are the main properties of the insulation material of power cables?
Answer:; It shall have the following main performances:
(1) High breakdown strength;
(2) Low dielectric loss;
(3) Very high insulation resistance;
(4) Excellent discharge resistance;
(5) It has certain softness and mechanical strength;
(6) The insulation performance is stable for a long time.
24. What are the regulations on traction strength when laying cables mechanically?
Answer: For copper core cable, when pulling the head, the allowable traction strength is 70N/cm; For aluminum core cable, the allowable traction strength is 40N/cm when pulling the head; If the wire mesh sleeve is used for traction, the allowable strength of the lead sheathed cable is 10N/cm;
Lead sheathed cable is 40N/cm.
25. What are the regulations for cable protection tubes?
Answer: (1) When the cable needs to be laid through the protective pipe, the inner diameter of the pipe should not be less than 1.5 times the outer diameter of the cable, and the inner diameter of the concrete pipe, clay pipe, asbestos pipe and cement pipe should not be less than 100mm;
(2) The bending radius of the cable pipe shall comply with the stipulations of the bending radius of the cable penetrated;
(3) Each pipe shall not have more than three bends at most, and there shall not be more than two right angle bends.
26. How to measure the outer diameter of the cable sheath?
Answer: Measure the outer diameter of the sheath and its average value at five points evenly distributed on the circumference of the sheath. The average outer diameter is the outer diameter of the sheath.
27. How to connect copper core cables with different sections?
Answer: Copper core cables with different cross sections can be connected with open weak back copper pipes by soldering, or pure copper rods can be connected into copper pipes according to the requirements of different cross sections by crimping.
28. Briefly describe the process of heat shrinkable manufacturing indoor terminal of 10KV cross-linked cable?
Answer:; (1) Preparation stage: check whether the heat shrinkable cable accessories are complete and the models are matched, and check the cable after checking and confirming whether there is moisture in the cable.
(2) Cut off the redundant cables, and determine the cable length according to the site conditions.
(3) Peel off the protective layer.
(4) Weld the grounding wire and weld the grounding wire on the steel strip.
(5) Fill the trident and wrap the sealant.
(6) Install the three core branch sheath, put the sheath into the root, shrink from the middle, first to the root, then to the finger.
(7) Strip the copper strip and outer semi conductive layer, strip the copper strip with the three core branch socket more than 20mm, do not damage the main insulation, and clean the semi conductive layer.
(8) Install the stress pipe, and heat shrink after butt joint of some supports at the nozzle end.
(9) Install the terminal blocks.
(10) Install insulating pipe.
(11) Install sealing pipe.
(12) Install phase color tube after phase verification.
29. What are the installation steps of indoor and outdoor prefabricated terminals?
Answer: (1) Put the cable in place, fix and clean the surface according to the preset position, peel off the sheath according to the instructions. If there are special needs, the stripping length of the outer sheath can be adjusted, and two groups of ground wires are led out from the copper tape and the outer sheath armor respectively.
(2) Measure the required size upward from the outer sheath opening, cut off the excess cable, insert a heat shrinkable three finger sleeve to the root of the three prong opening, and heat it in the middle. Measure the specified size upward from the upper opening of the finger sleeve (350~380mm for 35kv). Remove the excess copper strip (20 mm reserved), then reserve the preset position of the semiconductor, and crimp the outgoing line terminal for sealing.
30. The application of wires and cables is mainly divided into three categories:
1. Power system
The wire and cable products used in the power system mainly include overhead bare wires, bus bars (buses), power cables (plastic cables, oil paper cables (basically replaced by plastic power cables), rubber sheathed cables Overhead insulated cable ), branch cable (replacing part of bus), electromagnetic wire and electrical equipment wire and cable for power equipment.
2. Information transmission system
The wires and cables used for the information transmission system mainly include local telephone cables, television cables, electronic cables, radio frequency cables, optical fiber cables, data cables, electromagnetic wires, power communication or other composite cables.
3. Mechanical equipment, instrument system
This part is applied to almost all products except overhead bare wires, but mainly power cables, electromagnetic wires, data cables, instrument cables, etc.
31. Wire and cable products are mainly divided into five categories:
1. Bare wires and bare conductor products
The main features of this type of products are: pure conductor metal, without insulation and sheath layer, such as steel cored aluminum strand, copper aluminum bus bar, electric locomotive line, etc; The processing technology is mainly pressure processing, such as smelting, calendering, drawing, stranding/compression stranding, etc; The products are mainly used in suburban areas, rural areas, user main lines, switchgear, etc.
2. Power cable
The main features of this type of product are: extruding (winding) the insulation layer outside the conductor, such as overhead insulated cable, or several cores twisted (corresponding to the phase line, neutral line and ground wire of the power system), such as overhead insulated cable with more than two cores, or adding a sheath layer, such as plastic/rubber sheathed wire and cable. The main process technologies include drawing, stranding, insulation extrusion (wrapping), cabling, armouring, sheath extrusion, etc. The different process combinations of various products have certain differences.
The product is mainly used for the transmission of strong electric energy in power generation, distribution, transmission, transformation and power supply lines, with large current (tens of amperes to thousands of amperes) and high voltage (220V to 500kV and above).
3. Wires and cables for electrical equipment
The main characteristics of this kind of products are: a wide range of varieties and specifications, a wide range of applications, a large number of use voltages of 1kV and below, and constantly deriving new products in the face of special occasions, such as fire-resistant cables, flame retardant cables, low smoke zero halogen/low smoke low halogen cables, termite resistant, rat resistant cables, oil/cold/temperature/wear resistant cables, medical/agricultural/mining cables, thin wall wires, etc.
4. Communication cable and optical fiber (brief introduction)
With the rapid development of the communication industry in the past 20 years, the products have also developed at an amazing speed. From the simple telephone and telegraph cables in the past to thousands of pairs of voice cables, coaxial cables, optical cables, data cables, and even combination communication cables.
The structural dimensions of such products are usually small and uniform, and the manufacturing precision is required to be high.
5. Electromagnetic wire (winding wire)
It is mainly used for various motors, instruments and meters.
Derivative/new products of wires and cables
The derived/new products of wires and cables are mainly produced by using new materials, special materials, changing product structure, improving process requirements, or combining different types of products due to different application occasions, application requirements, equipment convenience and equipment cost reduction requirements.
Different materials are used, such as flame-retardant cables, LSZH/LSZH cables, termite resistant, rat resistant cables, oil/cold/temperature resistant cables, etc;
Change product structure, such as fire-resistant cable;
Improve process requirements, such as medical cables;
Combined products such as OPGW;
Convenient installation and lower equipment costs, such as prefabricated branch cables.
32. What inspections should be carried out after the construction of the busbar device?
Answer: The following inspections should be carried out:
(1) The processing, preparation and welding of metal components shall meet the requirements;
(2) All bolts, washers, cotter pins and other parts shall be complete and reliable;
(3) The bus configuration and installation frame shall meet the requirements, and the electrical distance between phases and ground shall meet the requirements;
(4) Porcelain, iron and gluing parts shall be complete, oil filled sleeve shall be free of oil leakage, and oil level shall be normal;
(5) The paint is complete, the phase color is correct, and the grounding is good.
33. In 35kv and below power cable joints, there are several methods to improve the electric field distribution at the sheath disconnection (please list five), and briefly describe the methods.
Answer: (1) Bell mouth expansion: pry up the edge of the lead package at the cutting point of the lead package to form a horn, and the edge should be smooth, round and symmetrical.
(2) Reserved blanket insulation: a section of blanket insulation paper is reserved between the lead sheath cut and the separation point of the cable core.
(3) Cut the semi conductive paper: cut the semi conductive paper below the bell mouth.
(4) Wrapping stress cone: wrap the insulation tape and conductive metal material into a cone to artificially expand the shielding layer to improve the electric field distribution.
(5) Equipotential method: for dry wrapped or cross-linked polyethylene cable head, wrap a piece of metal tape on the general insulation surface of each core and connect them together.
(6) Installation of stress control tube: for 35kv and lower heat shrinkable tube cable head, first wrap two layers of semiconductor tape from the end direction of the copper shielding layer of the wire core to the insulation profile of the wire core, and then fold the stress tube of corresponding specifications on the end of the copper shield, and heat shrink to form.
34. What requirements should the processing of cable supports meet?
Answer: (1) The steel should be straight without obvious distortion, the blanking error should be within 5mm, and the notch should be free of curling and burrs;
(2) The support shall be firmly welded without obvious deformation, and the vertical clear distance between the cross braces shall not exceed 5mm from the design deviation;
(3) The metal support must be subject to anti-corrosion treatment. If it is located in areas with damp heat, salt, fog and chemical corrosion, special anti-corrosion treatment shall be carried out according to the design.
35. List the cable racks you are familiar with.
Answer: welded E-frame, fabricated E-frame, bridge type cable frame, cable tray, hook type support, single cable support, etc.
36. What requirements should cable laying meet?
Answer: The following requirements shall be met:
(1) In terms of safe operation, try to avoid various external damages and improve the power supply reliability of cable lines;
(2) In terms of economy, consider the least investment;
(3) In terms of construction, the route of the cable line must be convenient for the maintenance after turning and putting into operation.
37. What are the insulating materials used to make cable terminals or intermediate joints?
Answer: There are insulating glue, insulating tape, insulating pipe, insulating gloves, insulating resin, etc.
38. Briefly describe the general operation procedure of cable head fabrication.
Answer: (1) Preparation before production: including ○ 1 reading the installation instructions; ○ 2 Inspect the site; ○ 3 Material preparation; ○ 4 Cable moisture test; ○ 5 Pre fabrication testing, etc.
(2) Manufacturing process of connector: including ○ 1 cutting off redundant cables; ○ 2 Stripping and cutting of cable protective layer; ○ 3 Conductor connection; ○ 4 Wrapping insulation (or shrink tubing); ○ 5 Install the connector housing; ○ 6 Inject insulating agent; ○ 7 Sealing treatment, etc.
(3) Electrical test after fabrication.
39. What requirements should the processing of cable protection pipes meet?
Answer: (1) The nozzle should be free of burrs and sharp corners, and should be made into a trumpet shape.
(2) After bending, the cable pipe shall be free of cracks and obvious dents, and its bending degree shall not be greater than 10% of the pipe outer diameter; The bending radius of the cable pipe shall not be less than the minimum allowable bending radius of the penetrated cable.
(3) The metal pipe shall be coated with anti-corrosion paint or asphalt table on the surface, and the galvanized pipe shall also be coated with anti-corrosion paint where the zinc layer is peeled off.
40. What requirements does the cable arrangement meet?
Answer: (1) Power cable and control cable shall not be configured on the same support.
(2) High and low voltage cables, strong and weak current control cables shall be configured in layers according to the required sequence, generally from top to bottom, but when high-voltage cables above 35kv are introduced into the cabinet, they can be configured from the bottom to the top to meet the bending radius.
41. What is the method of laying cables in the cable trench?
Answer: The method of laying cable in the cable trench is similar to that of directly buried cable. Generally, the pulley can be placed in the trench. After the laying, the cable can be placed at the bottom of the trench or on the support, and the cable label can be bound on the cable.
42. What are the common equipment for cable laying?
Answer: (1) The air compressor is mainly used to damage the road surface to prepare for the cable laying in the future;
(2) Electric winch or cable tractor, mainly used for pulling cables;
(3) The cable conveyor is used together with the tractor to overcome the huge friction and reduce the damage to the cable;
(4) Cable reel paying off support;
(5) Roller device;
(6) Anti twist, reduce the twist of wire rope;
(7) Cable reel braking device;
(8) Tensiometer.
43. What are the requirements for the installation distance of supports in the cable trench?
Answer: The cable is fixed on the wall of the cable trench and tunnel. When the horizontal device is installed, when the outer diameter of the cable is equal to or less than 50mm, a support should be added every 1m; Cables with outer diameter greater than 50mm shall be supported every 0.6m; Single cables arranged in a triangle shall be fastened with straps every 1 m, and fixed every 1~1.5 m for vertical installation.
44. How to handle the installation of power cable and control cable in the same tray?
Answer: Generally, power cable and control cable should not be laid in the same tray. When there are few cables and the control cable and power cable are laid in the same tray, they should be separated by a partition.
45. How to install grounding wires in cable tunnels?
Answer: The whole length of the tunnel and trench shall be equipped with continuous grounding wires, which shall be connected to all supports, and both ends shall be connected to the grounding electrode. The specification of grounding wire shall meet the design requirements. In addition to insulation requirements, cable lead wrapping and armouring shall all be connected with each other and ground wire, and cable rack and ground wire shall be coated with anti rust paint or galvanized.
46. What are the requirements for fireproof sealing of cable holes?
Answer: For large cable penetration holes, such as the place where the cable penetrates the floor, when using fire blocking materials to block, first apply four to six layers of fire retardant coating on the surface of the cable according to the actual situation, with a length of about 1.5m below the hole, and then process the fire-resistant materials into a plate holder fire blocking material with a certain strength, to ensure that it is firm after blocking and easy to disassemble when replacing the cable, It shall be sealed tightly without pores to effectively stop smoke and fire.
47. What inspections should be paid attention to before ignition of blowtorch?
Answer: The following inspections shall be carried out:
(1) Whether the pump leaks oil or gas, and whether the oil drum and nozzle leak oil or gas;
(2) Whether the oil volume in the oil drum exceeds 3/4 of the oil drum capacity, and whether the screw plug for oil filling is tightened.
48. What should be paid attention to when using blowtorch?
Answer: (1) The maximum oil injection volume of the blowtorch is 3/4 of the oil cylinder volume;
(2) The starting pressure should not be too high, and the flame can be used from yellow to blue after ignition;
(3) There shall be no combustibles around and the air shall be ventilated;
(4) Turn off the regulating switch first when it is out of service. After the fire is out, slowly loosen the oil hole cover to vent. After the air is discharged, loosen the regulating switch, and then loosen the hole cover after it is completely cooled;
(5) Kerosene burner and gasoline burner shall be used separately.
49. What is the purpose of manual hydraulic tong? How to operate?
Answer: The connection of two wires is usually to put the ends of two wires into a pressure pipe made of the same material, squeeze several pits with crimping pliers, so that the wires are connected together. When the handle is lifted up during crimping, the plunger moves outward, the lower cavity of the oil inlet valve generates vacuum, and the oil in the oil tank enters the plunger cavity. When the handle is pressed down, the plunger moves inward. When the oil is pressed, the oil inlet valve is closed, and the oil outlet valve is opened, so that the oil pressure enters the hydraulic cylinder, pushing the piston and the male mold. There is a pressure pipe between the male and female mold. When the depth of the pressed pit reaches a certain value, the oil return valve is opened, and the piston returns automatically. After pressing one pit, move the clamp and press another.
50. What are the main types of common low-voltage power cables according to their insulation and protective layers?
Answer: (1) Oil impregnated paper insulated lead (or aluminum) power cable;
(2) Non drip oil impregnated paper insulated power cable;
(3) PVC insulated PVC sheathed power cable;
(4) Cross linked PVC insulated polyethylene sheathed power cable;
(5) Cross linked PVC insulated PVC sheathed power cable;
(6) Rubber insulated power cable.
51. What are the categories of common insulating materials? For example?
Answer: (1) Inorganic insulation materials: mica, asbestos, marble, porcelain, glass, etc;
(2) Organic insulation materials: resin, rubber, paper, linen, cotton yarn, etc;
(3) Mixed insulating material: It is a kind of insulating material formed by processing the above insulating materials.
52. Under which circumstances is pipe laying adopted? What are the advantages?
Answer: Pipe laying is generally used at the intersection of other buildings, roads or railways, and sometimes in densely built-up areas. The main advantage is that it occupies less land, can bear large loads, and the cables do not affect each other, which is relatively safe.
53. What is the long-term allowable current carrying capacity of the cable?
Answer: The long-term allowable current carrying capacity of the cable refers to the current value when the cable conductor reaches the long-term allowable operating temperature after thermal stability when passing the specified current in the cable.
54. What factors determine the long-term allowable current carrying capacity of cables?
Answer: It is determined by the following three factors:
(1) Long term allowable working temperature of cable;
(2) Heat dissipation performance of the cable itself;
(3) Cable installation and surrounding heat dissipation conditions.
55. How many cable laying methods are there?
Answer: There are the following:
(1) Directly buried underground;
(2) Installed in cable trench;
(3) Installed in the underground tunnel;
(4) Installed on the internal wall or ceiling of the building;
(5) Installed on the bridge;
(6) Laid in the pipe;
(7) Laid under water.
56. How to connect cable ducts?
Answer: When connecting cable pipes, they must be connected with buckles and pipe joints. If welding is used, butt welding is not allowed. A section of thick pipe should be covered at the connection before welding to prevent welding slag from falling into the pipe.
57. What are the requirements for bending the cable core up and down when making the cable head?
Answer: When bending the wire core, the paper insulation shall not be damaged, and the bending radius of the core wire shall not be less than 10 times of the cable core. Special care shall be taken during fabrication to make the bending part of wire core evenly stressed, otherwise the insulating paper will be easily damaged.
58. Briefly describe the heat shrink sealing method of plastic cable.
Answer: The heat shrinking method is applicable to the sealing of medium and low voltage rubber and plastic cable joints and terminals, as well as non dripping and viscous impregnated insulated cables. Cross linked polyethylene type and silicone rubber type heat shrinkable tubes that can shrink uniformly after being heated are used. Put the pipe on the predetermined bonding and sealing part, and apply hot melt adhesive on the bonding part. When heated to a certain temperature, the heat shrinkable pipe will shrink, and the hot melt adhesive will melt at the same time. After natural cooling, a good sealing layer will be formed.
59. What should be paid attention to when bending cable protection pipe with electric pipe bender?
Answer: (1) The pipe bender shall be operated by personnel who understand its performance and are familiar with operation knowledge;
(2) Before use, it must be checked that the button, operating handle and travel switch are in good condition, and the pipe bender must be reliably grounded;
(3) Select the mold that meets the requirements, and determine the required bending radius;
(4) There should be sufficient activity scope around the construction site;
(5) When in use, it can work with load only after idling is normal. During operation, it is strictly prohibited to touch the rotating part with hands and feet;
(6) After the work is completed, the power shall be cut off in time to release the oil pressure.
60. What are the contents of the cable list and the meanings of the cable number?
Answer: The cable list is the basis for cable laying and construction guidance, as well as the archives for operation and maintenance. The number, starting point, model, specification and length of each cable shall be listed, and the total length shall be calculated by classification. The spare core of each cable shall also be listed for the control cable.
The cable number is a sign to identify the cable, so it is required that the number of the whole plant is not repeated, and has certain meanings and laws, which can express the characteristics of the cable.
61. What types of cable laying methods are currently used?
Answer: (1) Manual laying, that is to say, the laying is carried out according to the regulations under the coordination and command of one or more people by means of crowd strategy;
(2) Mechanized laying, that is, using rollers, pullers, conveyors, controlled by a synchronous power supply, is relatively safe;
(3) This method is adopted because of the combination of manpower and machinery. Some sites are difficult to construct due to many turns, and it is difficult to use all machinery.
62. What requirements should the control secondary circuit wiring meet?
Answer: (1) The wiring is correct according to the drawing;
(2) The electrical connection of the conductor shall be firm and reliable;
(3) The wires in the panel and cabinet shall be free of joints, and the core wires of the wires shall be free of damage;
(4) The end of the cable core shall be marked with its circuit number, which shall be correct, legible and not easy to decolorize;
(5) The wiring shall be neat, clear and beautiful, and the wire insulation shall be good and undamaged;
(6) Each side of each terminal should be connected with one wire at most.
63. What are the requirements for cable ducts?
Answer: (1) The distance from the top of the pipe row to the ground is 0.2m in the plant, 0.5m under the sidewalk, and 0.7m in general areas;
(2) Pipe row pits shall be installed at the change direction and branches, and additional pits shall be installed when the length exceeds 30mm;
(3) The pit depth is not less than 0.8m, and the manhole diameter is not less than 0.7mm;
(4) The drainage pipe shall have a drainage slope of 0.5%~1% inclined to the well pit.
64. What are the requirements for the resistance of cable conductor connection points?
Answer: The resistance of the connection point is required to be small and stable. The ratio of the resistance of the connection point to the conductor of the same length and section should not be greater than 1 for the newly installed terminal head and middle head; The ratio of terminal head to middle head in operation shall not be greater than 1.2.
65. What requirements should the design of cable joints and intermediate joints meet?
Answer: The following requirements should be met:
(1) High withstand strength and good conductor connection;
(2) High mechanical strength, low medium loss;
(3) Simple structure and strong sealing.
66. What is a cable fault? How many common types are there?
Answer: Cable fault refers to the fault that the cable line is forced to power off due to insulation breakdown during preventive test or insulation breakdown and wire burnout during operation. Common faults include ground fault, short circuit fault, broken wire fault, flashover fault and mixed fault.
67. How to deal with single-phase grounding fault of cable line?
Answer: Generally speaking, the damage of the cable conductor is only local for the single-phase grounding fault of the cable line. If it is a mechanical damage and the soil near the fault point is dry, it can generally be repaired locally by adding a dummy joint, that is, the cable core will not be sawn off, but the fault point will be sealed after the insulation is strengthened.
68. What tests and inspections should be carried out before laying power cables?
Answer: Before laying, check whether the model, specification and length of the cable meet the requirements and whether there is external force damage. The insulation resistance of low-voltage cable is measured with a 1000V megger, and the resistance value is generally not less than 10M Ω. The resistance value of high-voltage cable measured with a 2500V megger is generally not less than 400M Ω.
69. What should be paid attention to when laying cables in the main plant?
Answer: When laying cables in the main plant, attention should be paid to:
(1) The control cables leading to the central control room should be laid overhead;
(2) 6KV cables should be laid in tunnels or pipes, and overhead or pipes can also be laid at high groundwater levels;
(3) For 380V cable, when the cable at both ends is at zero meter, it is advisable to use tunnels, trenches or pipes. When the equipment at one end is on the top and the equipment at the other end is on the bottom, it can be partially overhead. When the groundwater level is high, it is advisable to overhead.
70. Where are the inner and outer shielding layers of power cables? What materials are used? What's the role?
Answer: In order to make the insulation layer better contact with the cable conductor and eliminate the increase of electric field strength on the conductor surface caused by the unsmooth surface of the conductor, the conductor surface is generally covered with an internal shielding layer of metallized paper or semiconductor paper tape. In order to make the insulation layer and the metal sheath have a good contact, an outer shielding layer is generally coated on the outer surface of the insulation layer. The material of the outer screen layer is the same as that of the inner screen layer, and sometimes the outer screen layer is bound with copper tape or braided copper ribbon.
71. Briefly describe the composition and properties of epoxy resin composites.
Answer: The epoxy resin composite is composed of epoxy resin added with hardener, filler toughener and diluent. It has the following performance:
(1) Have sufficient mechanical strength;
(2) Good electrical performance;
(3) Stable electrical performance;
(4) Sufficient adhesion with non-ferrous metals;
(5) Good corrosion resistance;
(6) When used outdoors, it shall be resistant to rain, light, humidity and heat.
72. Why must a return wire laid parallel to the cable be installed in the grounding mode of one end of the sheath of a single core cable?
Answer: In the cable line with one end of the metal sheath grounded, in order to ensure that the induced voltage in the protective sleeve does not exceed the allowable standard, a conductor laid in parallel along the cable line must be installed, and both ends of the conductor are grounded. This conductor is called return line. When a single-phase grounding fault occurs, the grounding short-circuit current can flow back to the central point of the system through the return line. Because the magnetic flux generated by the grounding current through the return line offsets the magnetic flux generated by the grounding current of some cable conductors, the induced voltage of the sheath during the short-circuit fault can be reduced.
73. How many projects can the cable project be divided into?
Answer: (1) Site transportation: including loading, unloading, transportation and empty return of engineering materials from the warehouse to the construction site.
(2) Local works: including road excavation, tunnel, trench construction, etc.
(3) Laying works: including laying, intermediate head fabrication, cover plate lifting, pipe laying, tide calibration, traction head fabrication, etc.
(4) Works at both ends: including the fabrication and installation of supports and suspension bridges and their foundations, the fabrication of terminal heads, the installation of oil pressure and signal devices, and the electrical performance test of various types.
(5) Stopping works: including production of oil filled cable plug, installation of oil supply tank, automatic drainage and signal device, etc.
(6) Grounding works: including insulation joint, transposition box, protector, grounding box installation, etc.
74. What inspections should be carried out for the acceptance of cable lines?
Answer: (1) The cable specification should meet the requirements, the arrangement should be neat, without damage, and the signs should be complete, correct and clear;
(2) The fixed bending radius of cable, relevant distance and wiring of metal sheath of single core power cable shall meet the requirements;
(3) The cable terminal and middle head shall be free from oil leakage and firmly installed. The oil pressure of oil filled cable and the setting value of gauge shall meet the requirements;
(4) Good grounding;
(5) The phase colors of cable terminals are correct, and the metal parts such as supports are painted completely;
(6) There shall be no sundries in the cable trench, tunnel and bridge, and the cover plate shall be complete.
75. What are the requirements for the positive sequence impedance measurement of cable lines?
Answer: The AC resistance of the cable conductor and the sum of the three same inductive reactances of the cable are called positive sequence impedance.
The positive sequence impedance of the cable line can generally be directly measured on the cable reel. Generally, a lower voltage is used during the measurement. Therefore, a step-down transformer is required for step-down. The step-down transformer is star connected, with a capacity of more than 10kVA. It has a wide range of voltage regulation. The AC power supply should be relatively stable during the measurement to ensure that the current during the measurement meets the specified requirements, The actual reading value of the voltmeter must be the voltage at the cable end, and the test current should be close to the long-term allowable current carrying capacity of the cable. When measuring the value of each meter, turn on the current and read the value of the three meters at the same time.
76. According to the Safety Regulations on Electric Power Production, what conditions must electrical workers have?
Answer: The following conditions must be met:
(1) The doctor has identified that the patient is in good health and has no disease hindering work;
(2) Have the necessary electrical knowledge, master the relevant regulations, professional technology and safe operation technology according to his position and work nature, and pass the examination;
(3) Master first-aid methods for electric shock.
77. What should be paid attention to during the transportation, loading and unloading of cables?
Answer: (1) In the process of transportation, loading and unloading, the cable and cable reel shall not be damaged. It is strictly prohibited to push the cable reel down directly from the vehicle. Generally, the cable shall not be transported and stored horizontally.
(2) Before transporting or rolling the cable reel, it must be ensured that the cable reel is firm, the cable is tightly wound, the oil pipe between the oil filled cable and the pressure oil tank should be fixed without damage, the pressure oil tank should be firm, and the pressure indication should meet the requirements.
78. What are the measures for cable fire prevention?
Answer: (1) Flame retardant cable is used;
(2) Adopt Fireproof cable Bracket;
(3) Fireproof coating shall be adopted;
(4) Fire partition walls and fire dampers shall be set at cable tunnels, mezzanine exits, etc;
(5) Overhead cables shall be kept away from oil pipelines and explosion doors, or local pipe threading or thermal insulation and fire prevention measures shall be taken.
79. What aspects should be considered when selecting the section of power cable?
A: The following aspects should be considered:
(1) Allowable working current of cable for a long time;
(2) Thermal stability in case of short circuit;
(3) The voltage drop on the line must not exceed the allowable operating range.
80. What are the advantages of power cable and overhead line?
Answer: (1) It operates reliably. Since it is installed in a concealed place such as underground, it is less damaged by external forces and has less chance of failure. Power supply is safe and will not cause harm to people;
(2) Small maintenance workload, no frequent patrol inspection;
(3) No need to erect poles and towers;
(4) It helps to improve the power factor.
Shandong Peninsula Cable Co., Ltd. is a professional Flexible fireproof cable Manufacturer, welcome to consult and purchase.