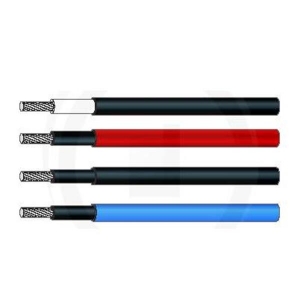
The cables used in the low-voltage DC transmission part of the solar photovoltaic power generation system have different requirements for the connection of different components due to different use environments and technical requirements. The factors to be considered generally include: the insulation performance, heat resistance and flame retardancy, aging performance, wire diameter specifications, etc. The connecting cable between the storage battery and the inverter is required to use multi strand flexible cable passing UL test, and try to connect as close as possible. Selecting short and thick cables can reduce the loss of the system, improve efficiency and enhance reliability.
Connection between solar cell modules PV cable Generally, the connecting cable attached to the component junction box is used for direct connection. If the length is not enough, special extension cable can also be used. According to the different power of components, this type of connecting cable has three specifications, namely 2.5m ㎡, 4.0m ㎡ and 6.0m ㎡. This kind of connecting cable uses a double-layer insulation sheath, which has excellent anti ultraviolet, water, ozone, acid, salt corrosion ability, excellent all-weather ability and wear resistance.
The properties of low smoke halogen-free flame retardant polyolefin irradiation materials and irradiation processing are special, so the following points should be paid attention to when irradiating photovoltaic cables: before irradiation, check whether the conductor of each cable head is fully grounded, and do not irradiate the cable without grounding. The absorbed dose of the insulation core and sheath during irradiation shall be subject to the qualification of the heat extension test. The surface of irradiated insulation core and sheath layer shall be smooth and clean without oil stain, with no obvious difference in color, no scratch, fuzzing, cracking, bubbles, etc., and the printing shall be clear and scratch resistant. The traction and take-up speed shall be coordinated with the beam current regulation action to avoid over dose or under dose when the irradiation speed is increased or decreased. The insulation core and sheath layer shall be fully discharged after irradiation, and shall be parked for 48h before moving to the next process.
Photovoltaic power stations have long sunshine duration, and their intensity of withstanding solar radiation is high. The solar radiation contains a variety of rays, especially ultraviolet ray, which can accelerate the aging of cable insulation and protective layer. Most of the cables in the photovoltaic power station are laid bare. In most cases, the cables from the solar modules to the combiner box or even to the inverter are directly laid bare. This requires that the cables must be able to withstand the radiation of sunlight and ultraviolet rays, and ensure that they can work normally for a long time under the vertical radiation of sunlight and ultraviolet rays. Therefore, qualified photovoltaic cables can work normally for a long time under the conditions of sunlight and ultraviolet radiation, while the insulation and sheath of conventional cables will accelerate aging under the conditions of sunlight and ultraviolet radiation, leading to the problems of reduced or invalid insulation performance and reduced protective effect of sheath.
Compared with copper wire, aluminum wire connection is more dangerous because of the following reasons: copper aluminum joints are prone to electrochemical corrosion; The surface of aluminum wire is easy to be oxidized in air; Easily corroded by hydrogen chloride; High expansion coefficient; In addition, copper has absolute advantages over aluminum in conductor performance. The conductivity of aluminum is only about 60% of that of copper conductor, and that of aluminum alloy conductor is even worse; In terms of oxidation and corrosion resistance, the chemical property of aluminum is much more active than that of copper, so the oxidation and corrosion resistance of aluminum conductor is much worse than that of copper conductor, and the fire probability of aluminum conductor is about 10 times that of copper conductor; From the perspective of thermal expansion, the linear expansion coefficient of aluminum conductor is far greater than that of copper conductor. The use of aluminum questions will lead to poor contact after thermal expansion and cold contraction, or even accidents such as loose contact, oxidation and heating, and will lead to a vicious cycle.