The mold is the device for product shaping and the last hot pressing device in the whole process of plastic extrusion. Its geometric shape, structural form and size, temperature and pressure directly determine the success or failure of cable processing. Therefore, the design, selection and thermal insulation measures of any extrusion product mold are highly valued. When extruding the insulation layer and sheath layer of wires and cables with a plastic extruder, the mold is the key to control the thickness of the plastic extrusion coating.
The general extrusion dies can be divided into three types according to the extrusion mode: extrusion type, extrusion tube type and semi extrusion tube (extrusion) type. The matching method is shown in the figure below:
Extrusion die: There is a certain distance between the mold core and the inner side of the sizing area of the mold sleeve. If the final shaping of the product is achieved by pressure, the plastic is directly extruded onto the wire core or cable core through extrusion, and the extrusion is tight and firm, with flat and smooth surface. However, it is easy to be eccentric, its service life is not long, its mold matching requirements are high, and the bending performance of the extruded core is poor. Suitable for extruding small size wire cores; The extruded core shall be compact and the appearance shall be round and even; And plastic stretching is relatively small.
Extrusion die: Mold core has "Long nozzle", when matching, the core nozzle of the mold is generally flat with the sleeve mouth of the mold, thus forming an extrusion die. It makes use of the extensibility of plastics. Compared with extrusion dies, it has the advantages of high efficiency, easy deflection adjustment, good bending performance of the extruded wire core, long service life, strong die matching interchangeability, etc., but it is inferior to extrusion dies in terms of extrusion compactness, extrusion quality, etc.
Semi extrusion die: Also known as semi extrusion die, the die core has "Short nozzle": generally, the core nozzle is at 1/2 of the die sleeve sizing area. The semi extrusion die is basically the same as the extrusion die, except that the length of the die nozzle is shorter than the extrusion die, and the length of the sizing zone of the die sleeve is also slightly shorter than the extrusion die. It absorbs the advantages of the extrusion die and the extrusion die, improves the disadvantages of the above two dies, and has wide applicability. However, when the wire core has poor flexibility or the wire core is bent, this kind of die should not be used for extrusion.
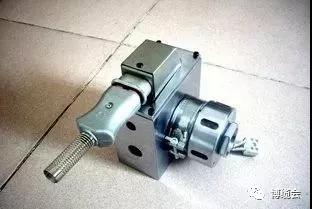
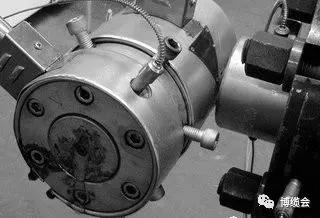
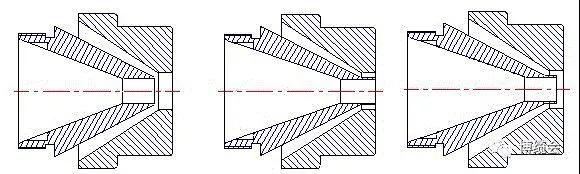
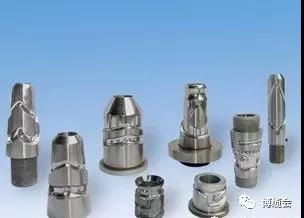
The most common compression molding mold in the cable industry is the profiled pressing wheel, which is suitable for pressing multi-core cable cores. According to its purpose and angle, it can be divided into: 180 ° two core cable, 120 ° three core cable, 90 ° four core or 3+1 core cable and 3+2 or 4+1 core cable. It also subdivides 3+1-core, 3+2-core and 4+1-core cables into 90 °, 100 °, etc. After the round wire core is compacted by the profiled pressing wheel, the shape we designed can be obtained, thus reducing the outer diameter of the cable and saving materials.
The relationship between the design area S of the pressing wheel and the calculated area S1 of the wire core is: S=S1/k K - filling coefficient, equal to compression coefficient k1 × elongation coefficient k2. According to the size of core section : 70mm2 and below, 0.84 for k1 and 1.03 for k2; 120 mm2 ~ 185 mm2, 0.83 for k1 and 1.03 for k2; For 240 mm2 and above, take 0.85 for k1 and 1.02 for k2.
The above are all the empirical values of national marking cores for reference. In view of the current situation of diversified conductors, the k value must be verified before being known. The key factors affecting the S value are the large arc radius R and the sector height H. Since the calculation formula of R and H values is rather complicated, I will not elaborate here. You can refer to the relevant information on page P1133 of Volume I of the Wire and Cable Manual.