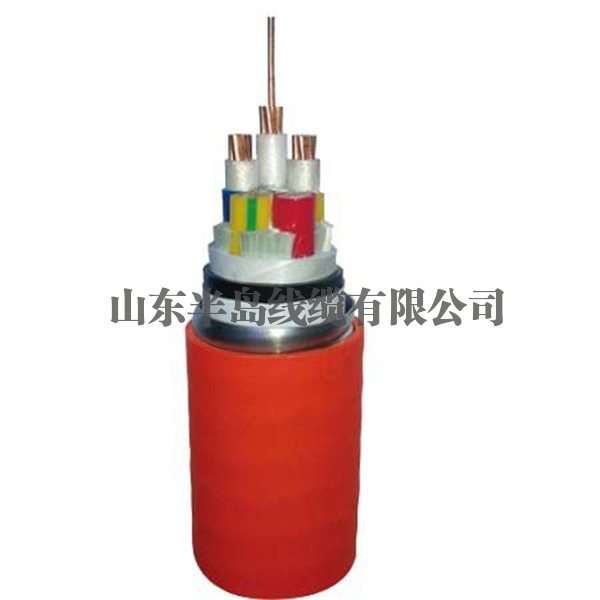
Cause Analysis of Blackening of Wire and Cable Copper Wire
Causes of copper wire blackening
(1) The area of the drawing emulsified oil pool is small, the return pipe is short and sealed, resulting in slow heat dissipation and high emulsion oil temperature.
(2) It is caused by copper wire annealing. First, the cooling water for continuous withdrawal is generally tap water and groundwater. Because the water quality varies from place to place, the PH value of water quality in some areas is low, only 5.5~5.0 (normally 7.0~7.5). The antioxidant oil film in the original emulsion has been cleaned, and the annealed copper wire is easy to oxidize and blacken; Second, the finished copper wire drawn by ordinary wire drawing machine is annealed on another annealing line, and the cooling water does not use antioxidant, so the anti oxygen time is short, and oxidation and blackening will soon occur;
(3) Some old factories still use annealing cylinders for annealing, and the following reasons can also cause oxidation and blackening: First, the nuts of the annealing cylinder are not tightened, and air leaks after flushing carbon dioxide or high-purity nitrogen; The second is that the copper wire temperature out of the cylinder is too high, exceeding 30 ℃; Third, the maintenance of drawing emulsion is not enough, and the PH value is too low; These situations are common when the temperature is high in summer, and the emulsion will be lost if it is used continuously. If the temperature is high, the loss is fast. If new crude oil is not replenished in time, the fat content is low at this time. In addition, the temperature of the emulsion may also exceed 45 ℃, which is easy to cause oxidation and blackening.
(4) Another situation is that because high-speed wire drawing is widely used at present, its speed is increased and the relative heat dissipation time is reduced, which brings a certain space and time for oxidation. Therefore, it is recommended that manufacturers pay more attention to the fat content of emulsion, the use temperature, Whether the PH value is appropriate or not. In the yellow and rainy season of spring, bacteria multiply rapidly, so bactericides and mildew inhibitors can be used. In summer, antioxidants can be used to solve the problem of oxidation and blackening.
Causes: 1. The deformation of the finished mold is too small;
2. The periphery and front of the mold insert are not sealed well.
Solution: add a rubber pad in the outlet direction of the finished mold, and then screw down the finished mold to solve the problem of oil leakage.
It is a common mistake that the deformation of the finished mold is too small. The single mold deformation needs a minimum deformation, so the pressure generated can be greater than the yield limit of the metal, so that plastic deformation can be achieved, the size can be stable, and the single wire surface can have the light generated by cold drawing.
Causes of coil blackening
In life, we often use various products that use coils, such as motors, speakers, hearing aids, remote control toys, wireless chargers, power switches, computers... The coil blackening is due to the oxidation of copper wire. The main material of the coil basically uses copper wire, while the metal will be oxidized, so we will see the blackening of the coil.
1、 Technical reason: Most manufacturers in China used to use universal copper rods, and the copper content can reach 99.95%, but even today, there is still O in copper. The reason is that copper itself is not oxygen free copper, and the surface of copper will inevitably be oxidized when contacting with air during processing. Up to now, the advanced production technology of oxygen free copper has been introduced in China, as well as the oxygen free copper production technology developed by China itself, making the entire copper wire industry use oxygen free copper, which has undoubtedly greatly improved the blackening problem of copper wire. However, due to the processing of copper rod, especially the application of toughening process and the poor storage conditions of finished copper wire core, the copper wire itself will still have slight oxidation.
2、 Material problem of insulation layer: insulation paint can be divided into five categories: impregnating paint, enamelled wire paint, covering paint, silicon steel sheet paint, anti corona paint, etc. The impregnating varnish is used to impregnate the motor and electrical coil. The impregnating varnish can fill the gaps and micropores in the insulation system, form a continuous paint film on the surface of the impregnated material, and bond the coil into a solid whole, effectively improving the integrity, thermal conductivity, moisture resistance, dielectric strength and mechanical strength of the insulation system. Secondly, it also plays the role of heat dissipation. If the insulating paint is soaked, the dried coil can be regarded as a whole, and the internal and external heat can be easily transmitted, thus playing the role of heat dissipation. At present, China's impregnating varnish, insulating oil production process, preparation method, and technical data of zhuanli formula are relatively backward. The impregnating varnish produced and processed basically only plays a temporary role, and will fall off and become invalid after a long time.
3、 Problems in use: In the process of using the coil copper wire, we often encounter such problems as collision and friction, slow washing, large amount of water contacting the coil, use of waste oil for lubrication, resulting in the destruction of residues and insulation layer on the surface of the conductor, and the oxidation of the conductor during subsequent processing;
4、 Copper wire annealing process: copper wire annealing refers to a kind of metal heat treatment in which the copper wire is slowly heated to a certain high temperature and then kept for a period of time, and then cooled at a corresponding rate. Copper wire annealing can reduce hardness, improve machinability, eliminate residual stress, stabilize size, and reduce deformation and crack tendency; Refine the grain, adjust the structure and eliminate the structural defects. However, once the temperature is higher than 50 ℃ during the production process, the specified air extraction time is insufficient, the SO2 content is high, and the protection gas is impure, which will lead to insufficient annealing. After a period of time, the copper wire will be easy to blacken.
The blackening of coil copper wire is caused by many factors, not only the above four factors, but also the state of the copper wire itself, coil processing technology, vulcanization process, coil structure, formula, coil production environment and many other factors.
Rubber sheathed cable Causes of copper wire blackening
The blackening of copper wire is caused by many factors, not only the rubber formula, but also the state of the copper wire itself, rubber processing technology, rubber vulcanization technology, cable structure, sheath rubber formula, production environment and many other factors.
1. Cause Analysis of Rubber Stickiness and Copper Wire Blackening
1.1 The reason for the copper wire itself In the 1950s and 1960s, most domestic manufacturers used ordinary copper rods with 99.99% copper content, all of which were oxygen copper rods. The production method was to heat copper ingots and make them into black copper rods after multiple passes of rolling. The copper rods were made into relatively fine copper wires through large, medium and small drawing. Because copper itself is not oxygen free copper, oxidation is inevitable on the surface of copper wire during processing. By the 1980s, the advanced production technology of oxygen free copper rod and the self-developed oxygen free copper rod production technology were introduced in China, which made the entire wire and cable industry use oxygen free copper rod, which undoubtedly improved the blackening problem of copper wire. However, due to the processing of the copper rod, especially the mastering of the toughening process, and the poor storage conditions of the processed copper wire core, the copper wire core itself has been slightly oxidized, which is one of the reasons for the blackening of the copper wire.
1.2 Reasons for rubber formula In 1950s, natural rubber and styrene butadiene rubber were used for rubber insulation. Since the insulating rubber is in direct contact with the copper wire, sulfur cannot be directly used as the vulcanizing agent. Even if very little sulfur is used, the copper wire will be blackened. Some compounds capable of decomposing free sulfur, such as accelerator TMTD and vulcanizing agent VA-7 mentioned above, must be used. At the same time, some vulcanizing accelerators must be used to improve the vulcanization speed and degree, so as to ensure the physical and mechanical properties and electrical properties of the insulating rubber. However, the elasticity, strength and permanent deformation of insulating rubber are inferior to those with sulfur (if the blackening of copper wire is not considered). Decades of practice have proved that TMTD cannot solve the problem of copper wire blackening. In addition, the insulating rubber should have various colors. Red, blue, yellow, green and black are the basic colors. The appearance of these colors will also make the rubber sticky
And copper wire blackened. The main fillers in the formula are light calcium carbonate and talcum powder. Due to the price relationship, some manufacturers use calcium carbonate and talcum powder which are very cheap to reduce costs. These fillers have coarse particles, high content of free alkali and many impurities, so their physical and mechanical properties are poor, electrical properties are poor, and copper wires are prone to blackening. Other factories use active superfine calcium carbonate to improve the physical and mechanical properties of insulating rubber, while most of the active calcium is treated with stearic acid, which is also the reason why the copper wire blackens. The use of vulcanizing agent VA-7 can improve the blackening of copper wire, but due to insufficient vulcanization, the permanent deformation of rubber is large, which will cause the rubber to become sticky. Especially after adding accelerator ZDC, the curing speed is increased. In order to prevent scorching, accelerator DM is also added to delay scorching time. From the structure of accelerator ZDC, a metal zinc is connected between two connected sulfur in the TETD structure. The structural formula is: S S H5C2 ‖‖‖‖‖‖‖‖ H5C2 > N-C-S-Zn-S-C-N < H5C2 H5C2, which is very close to the TETD structural formula S S H5C2 ‖‖‖‖ H5C2 > N-C-S-S-C-N < H5C2 H5C2. It is impossible to avoid the blackening of copper wires with structures similar to those of Tyuram in the formula, which may take a little longer, But it was not fundamentally solved.
2. Analysis from wire and cable structure
2.1 The catalytic aging of copper is an important reason for the stickiness of rubber. The former Soviet Union's Cable Science Research Institute has proved that copper penetrates into the insulating rubber from the contact with rubber during vulcanization, and the insulating rubber with a thickness of 1.0-2.0mm contains 0.009-0.0027% copper. As we all know, trace copper has a great destructive effect on rubber, which is what we usually call the catalytic aging of heavy metals on rubber. In the process of insulation vulcanization, thiuram precipitates some free sulfur and reacts with copper to form an active copper containing group: CH3 │ CH2-CH-C-CH2 - ││││ S S ││ Cu Cu During aging, the weak S-S bond breaks, forming an active copper containing group: Cu-S -, which acts with rubber and oxygen to destroy the long bond molecules of rubber, making the rubber soft and sticky, and is a combination of low molecular chains. The French Rubber Research Institute also pointed out that if the rubber contains harmful metals, such as copper, manganese and other heavy metal salts, the rubber will become sticky regardless of the type of accelerator.
2.2 The migration of sulfur in rubber sheathed cables to the surface of insulating rubber and copper wire scientists in the former Soviet Union confirmed the possibility of sulfur diffusion in cable sheath rubber by using radioisotopes. In natural rubber based vulcanizates, the diffusion coefficient of free sulfur is about 10-6cm2/s at 130-150 ℃. For continuous vulcanization plants, when the sheath rubber is vulcanized, the diffusion coefficient is greater when the temperature is between 185-200 ℃. Due to the diffusion of free sulfur in rubber sheath, the structure of thiuram rubber was changed, and polysulfide bond may be formed. These polysulfide compounds migrate through chemical decomposition and combination, that is, "chemical diffusion". As a result of migration, not only can the structure of the insulating rubber be changed and its heat resistance be reduced, but also the sulfur reacts with the copper surface to form copper sulfide and cuprous sulfide, resulting in blackening of the copper wire. Conversely, copper sulfide and cuprous sulfide accelerate the aging of rubber, and lead to the occurrence of tackiness.
3. Reasons for processing technology
3.1 The reason for rubber processing is that in the insulation formula based on the combination of natural rubber and styrene butadiene rubber, natural rubber needs to be refined to improve the plasticity of rubber. Some large factories use internal mixer for plasticizing in order to increase their output, and also add a small amount of chemical plasticizer -- accelerator M to improve plasticity. If the molding temperature and the temperature of raw rubber during rubber filtering are not well controlled, and a high temperature of more than 140 ℃ occurs, when the raw rubber is placed on the open mill and slowly passes through the drum, and the accumulated rubber on it is affected by hot oxygen and accelerator M at the same time, it will be found that the rubber surface seems to be coated with a layer of oil. In fact, the rubber molecules are seriously broken under the promotion of chemical plasticizers, A relatively soft and sticky rubber with smaller molecular weight is produced. Although the insulating rubber was mixed with styrene butadiene rubber later, these small molecular weight natural rubber was evenly dispersed in the rubber compound. After these rubber compounds were extruded and wrapped on the copper wire for continuous vulcanization, there may be no problem at that time, but it has buried a hidden danger for the rubber to stick to the copper wire. That is to say, these small molecular weight natural rubber will first appear local copper wire sticking. The process of adding vulcanizing agent and accelerator to insulating rubber is also very important. Some small factories add vulcanizing agent on the open mill, that is, pour the cans containing vulcanizing agent into the middle of the drum, with many in the middle and few on both sides. When the vulcanizing agent is eaten into the rubber, the number of times of turning the triangle is less, which will cause uneven distribution of the vulcanizing agent in the rubber. In this way, during extrusion and continuous vulcanization, it is easy to blacken the copper wire where there are a lot of vulcanizing agents. After a long time in the blackened place, the rubber will stick to the copper wire.
3.2 The reason for the vulcanization of insulating rubber is that some enterprises, in order to pursue output, have a continuous vulcanization pipe only 60 meters long, a steam pressure of 1.3 Mpa, and a vulcanization speed of 120 meters/minute, so that the stay time of insulating rubber in the pipe is only 30 seconds. The rubber itself is a bad conductor of heat, and the surface temperature of the insulated wire core is greater than 190 ℃. When the temperature is transferred to the inner rubber in contact with the copper wire, it is absorbed by the copper wire. When the copper wire is heated to a temperature close to the inner rubber, the vulcanized rubber wire core has already left the vulcanization tube. In this way, the temperature of the inner rubber is relatively low, about 170 ℃. After staying for a few seconds, the rubber leaves the vulcanization tube and goes into cooling and winding up. The insulating rubber will not be vulcanized enough. In order to achieve sufficient vulcanization. The amount of accelerator TMTD (used as vulcanizing agent) is as high as 3.4%. The excess vulcanizing agent also releases more free sulfur during vulcanization. In addition to cross-linking rubber molecules, there is also excess free sulfur. This is the reason for the blackening of the copper wire surface.
In short, it is still difficult to solve the problem of copper wire blackening. Every process from copper wire to rubber must be taken seriously to achieve better results. The selection of rubber type and the adoption of curing system are still the key problems. The solution of this problem needs to go through the test of time.
Shandong Peninsula Cable Co., Ltd. is a professional Fireproof cable Manufacturers, welcome customers to consult.